Type 1: Fire-Resistive structures are constructed of concrete and protected steel (steel coated with a fire-resistant material). These are typically modern high rise construction and are designed to hold fire for an extended amount of time in order to keep the fire at bay at the point of origin.
Concrete as a building material has been used since Roman times. even if you casually follow the construction of a new building, you will have probably noticed yards and yards of it being poured. Concrete by itself is best in compression, That is why steel rebar is placed within it. concrete also takes about 28days to fully cure, and it shrinks while it cures. Finally, during that curing period, it still requires some support. the effect of this is you will not see adjoining slabs poured too closely together.
When we look at the basic process from the ground up, footings sit on Bedrock, Columns sit on footings, and floors are supported by columns. Our example sits on bedrock which makes the foundations relatively simple.
On the right is one of the footings being poured. this one sits under several columns and elevator shafts, so it is quite large, however most of the individual columns had their own footing. A rebar cage is used as well, however this is mostly to control shrinkage and tie in the columns as this is entirely compressive concrete.
Columns are relatively simple. the footing has rebar protruding rebar up through the top of its finished level. A Rebar cage is attached to this, and a form placed around it. The form is typically a premade structure that is in 2 pieces and bolts together at opposite corners. when the blots are released, the form comes off. the Column is then poured. In this case, the rebar in the columns is placed towards the out side edges to resist tension forces being applied to the column horizontally. (eg. wind loads)
After the Columns have cured, and the formwork removed, Staging can be set up for the floor slabs. These typically consist of shoring, with large timbers across the top supporting the form boards. there is also a larger form used for flooring which consist of trusses with adjustable legs, shoring beams and forming deck all as one piece. These can be setup, and then moved as a unit.these are known as flying forms, and at right is one being moved by a crane, you can see the trusses, and form boards. Flying forms have adjustable feet, and once the slab is cured, they can be lowered, set on rollers and moved out.
On top of the slab form work can be laid the rebar, and any Electrical or plumbing services to be run through the slab. the edge is formed off, and, if an adjoining section of slab is to be poured, keyed. Adjoining slabs cannot be poured right away due to shrinkage. before pouring an adjoining slab, one must wait for the first section to cure.
![]() |
On the Left, Poured Columns with forming for the Drop Panels in place, and on the left Columns to be poured |
When we look at a floor slab, we are typically dealing with a 2 way spanning slab, also known as a flat slab. In a 2 way slab, the beams to support it become flattened and integrated into the slab itself. When looking at the rebar layout, you will typically see a denser pattern running an a Square pattern between the columns and less rebar in the Center. The issue with a Flat slab is that the shear forces at the column can result in a failure of the slab. As a result a Drop Panel is used at column connections to ensure there is more material to strengthen the connection . You can see examples of these in the photo above, which shows the drop panels in place. The Slab may also be poured with a Stronger mix of concrete at these shear points. You will notice in the photos that the drop panels were poured first. These panels are poured with 50mpa Concrete, whereas the rest of the floor is done with 30mpa concrete.
The load on a slab typically comes from above. the load causes it to bend, so the top is in compression (Which concrete is good at) and the bottom in tension. this is why rebar is placed at the bottom of the slab – the rebar works in tension, so it is placed in the area subject to tension.
![]() |
Note the deeper area with the denser rebar – those are the beam portions. |
There is also a one way slab, where there is a beam supporting the slab. These require more depth, but can span wider distances. I believe this type of slab is being used on the Argyle street level. The beam and slab are still poured as one piece, however there is a difference in depth.
Spanning slabs need support until fully cured. This is typically accomplished with Large timbers or jack posts.
![]() |
The floor slab, prior to being poured |
The final slab type, is actually found at the very bottom, and this is the slab on grade. This is supported by a gravel base which sits on bedrock for drainage, and contains a thin wire mesh for tensile support.
A slab on grade simply needs to be formed to give it a clean Edge.
![]() |
Wall Form. Note the bracing. the empty holes are for the form ties. |
Walls are typically poured in a similar manner to a column, however their forming takes a different shape. The form boards typically are supported by vertical members, which are then reinforced by horizontal members. this makes for a rigid surface that wont deflect under the load of the wet concrete. Form ties are also used to hold the forms an even distance apart. these are eventually snapped off with the rod remaining within the concrete wall. These ties are what are responsible for the round indents you see periodically in a concrete wall.
Concrete can be placed via a variety of methods. A truck can simply pour it out, it can be placed with a Crane and bucket, or it can be pumped.
Pumping offers the most flexibility, and offers a continuous pour a distance away from a delivery truck. Truck mounted pumps come in various sizes.
![]() |
A Placing arm allows pumped concrete to be distributed across a slab. Note the Drop Panels have been poured and finished first |
A truck mounted pump can pump directly to a location (As above), or can also supply a placing arm, as is the case below. Note the arm in this case was pumped by a much smaller pump truck, and was fed by a fixed pipe, running between the arm and the truck.
Trailer based pumps are also available, and can be used to supply a fixed tower based placing system, which climbs as the structure goes up.
![]() |
Pouring a Slab, From right to left, Placing concrete with an arm, shovel/rake to depth, screed with a power screed, and finally hand float. |
After the concrete is poured, it is Vibrated to remove air bubbles, raked and secreted to a level surface. the vibration is a key part of pouring concrete and ensures it flows evenly and cures without air pockets throughout. The vibrator is basically a hose on the end of an electric or gas powered tube that spins to produce a vibration, which causes the concrete to settle.
As Concrete cures, the watery “cream” floats to the surface. this can be first hand floated and eventually mechanically floated to give a clean surface.
the underlying concrete structure is then covered in studs and drywall. which contain services.
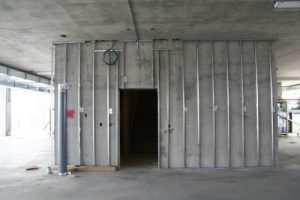
Steel Buildings
Construction with steel is very similar to concrete. typically a concrete footing will contain a steel embed plate that is cast into the concrete, and the posts and beams will be bolted and welded to the plate.
like traditional house framing, once the main posts and beams are erected, trusses are then laid that can support the floor.
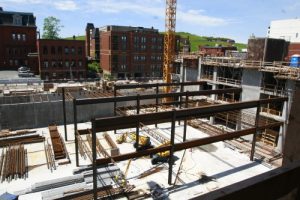
these trusses are the slenderest and most lightweight component, and support a steel deck, which then has a steel mesh laid on top, which is then has a concrete slab poured on top to achieve the finished floor.
One thing to note, is none of this steel has had a fire proof coating applied. When that occurs, the steel takes on a fuzzy appearance.
Exterior Walls
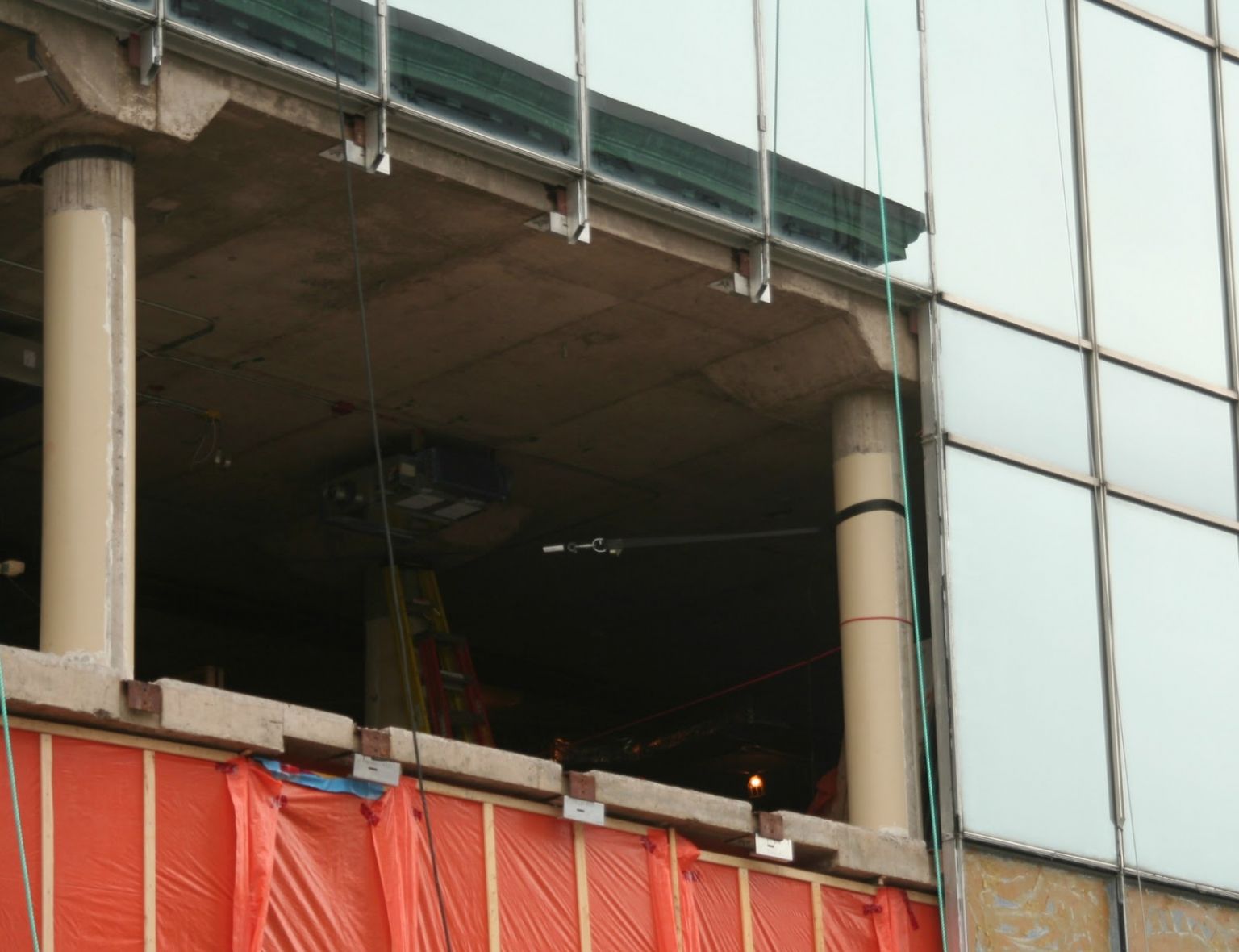
many highrise commercial structures use Curtain walls are bolted to the outside of a structure. In the Photo Above, you can clearly see how slender the exterior wall is versus the structure of the building.
A curtain wall is an outer covering of a building in which the walls serve no structural purpose, but merely keep the weather out and the occupants in. As the curtain wall is non-structural it only needs to resist forces acting on it.
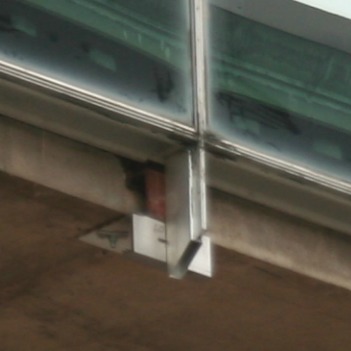
The curtain wall does not carry any dead load weight from the building other than its own dead load weight. The wall transfers horizontal wind loads that are acting on it to the main building structure through connections at floors or columns of the building. A curtain wall is designed to resist air and water infiltration, sway induced by wind and seismic forces acting on the building. (above) you can see one of the attachment points of the Curtain wall to the Structure.
While the example above is glass, Concrete panels and Aluminum panels can also be hung in the same way. One key point about curtain walls is that there is a gap between the Curtain wall and the slab. this gap needs to be sealed against fire, or fire can spread between floors.
If a curtain wall is not used, a stud wall is typically built between the slabs. This method is more common for residential buildings with balconies. The stud wall is then insulated, sheathed, and an exterior cladding applied.